3.7 Printing unit debugging principle
1. The impression cylinder is the reference for the printing unit
The roles and adjustments of the various components of the printing unit have been discussed separately. What kind of relationship should be put together? If the match is inaccurate, how should we adjust it? The following is a detailed analysis of the basic structure of a printing unit, as shown in Figure 3.32.
Because the impression cylinder plays a role in transferring the paper, its position change directly affects the accuracy of overprinting. Once the cooperation relationship of the transfer path is determined, the position of the impression cylinder is completely determined.
From the perspective of the transfer of images and texts, the graphic on the plate is transferred to the impression cylinder by a blanket cylinder. Since the graphic on the plate cannot always be kept in one position, it is usually required to use a plate-making mechanism or a plate-adjustment device to calibrate, and the position of the plate cylinder cannot be adapted by changing the position of the impression cylinder.
From the point of view of the contact of the roller, it is necessary to transfer the graphic, and the roller should be in line contact or even surface contact, that is, the axes of the rollers should be mutual lines. Since the position of the impression cylinder has been determined, the axis of the blanket cylinder can only be adjusted relative to the impression cylinder, and the axis of the plate cylinder can only be adjusted relative to the blanket cylinder.
From the perspective of clutch pressure, the position of the blanket cylinder is determined due to the interaction between the clutch pressure and the pressure regulator. Once the pressure is different, the position of the blanket cylinder is different, but the cylinder cannot change with the position of the blanket cylinder.
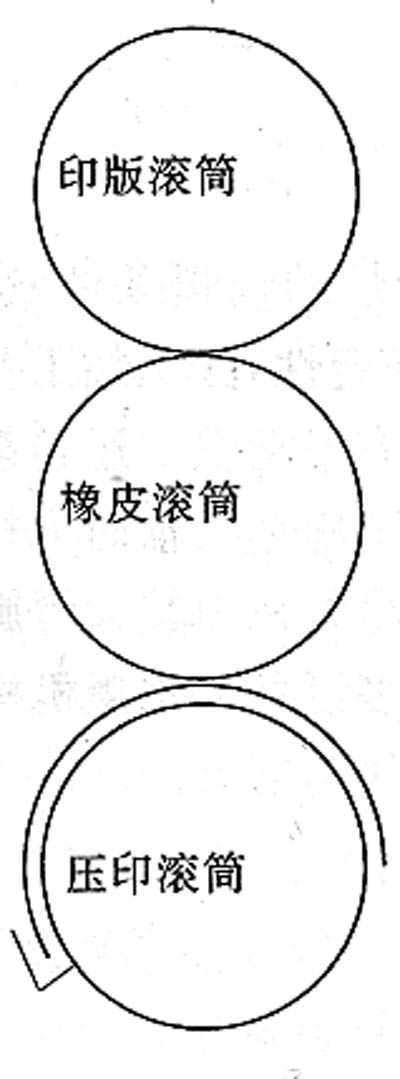
To sum up, in the printing unit, the position of the impression cylinder is not adjustable, that is, the absolute reference of the printing unit. The blanket cylinder can be adjusted relative to the impression cylinder, but it cannot be adjusted with respect to the plate cylinder. Therefore, the blanket cylinder is the first relative reference. Similarly, the plate cylinder can be adjusted relative to the blanket cylinder and not to the ink fountain mechanism, so the plate cylinder is the second relative reference.
From the pressure adjustment point of view, when it is found that the pressure between the blanket cylinder and the impression cylinder is not suitable, it should be adapted by changing the position of the blanket cylinder; when it is found that the pressure between the plate cylinder and the blanket cylinder is not suitable, Adjust the ink mechanism to meet the requirements.
From the point of view of time and displacement coordination, when it is found that the fit of the blanket cylinder and the impression cylinder is not suitable, it should be adapted by changing the gear position of the blanket cylinder; when the cooperation between the plate cylinder and the blanket cylinder is found to be inappropriate, It should be adapted by changing the position of the plate cylinder gear. When it is found that the ink printing mechanism (such as the pulsing of the tandem roller) is improperly matched with the plate cylinder, the requirements should be satisfied by changing the position of the ink fountain mechanism.
The mutual adjustment between the various components mentioned above is performed under the condition that the working condition of each component itself is completely normal. This should not be taken into account when adjusting, ie, check every component, such as the unevenness of the blanket. In particular, we must pay attention to: Absolutely irreversible, that is, to reverse the benchmark.
Whenever the printing unit is adjusted, it is necessary to ensure the parallelism of the rotation axis, which is an important condition for its stable operation. Therefore, the pressure of the contact surface should be as uniform as possible.
2.Rotary shaft axial movement
During the printing process, due to the axial force, the drum may be axially traversed. Once axially strung, it will cause dot slip or ghosting. The axial direction of the roller is generally controlled by the lock nuts at both ends. From the point of view of the installation and processing of the thrust bearing, it is impossible to be completely uniform, a certain gap is needed to make it relatively operable, and another one may cause the bearing to be stuck due to heat or pressure elongation of the rotary shaft. From an aspect point of view, there must be a certain amount of axial stringing during commissioning. Different manufacturers of this string size is not the same. Generally less than 0.03mm. Without affecting the rotation of the bearing, the smaller the amount of stringing, the better. The usual adjustment method is: After the lock mother is fully locked, and then reverse one half or one third of the circle can be more accurate method can be used dial indicator to detect.
3 radial runout of the rotary axis
The radial runout of the rotary shaft is mainly caused by the machining and installation errors of the machine. The radial runout of the drum is a major indicator of factory inspection. Once the radial runout of the roller is found to be too large, the cause must be ascertained, whether it is a failure or an installation problem. The radial jump of the drum affects the stable operation of the machine, at the same time it also causes the printing pressure to be unstable, resulting in a series of printing failures. Therefore, it is necessary to minimize the radial runout of the drum.
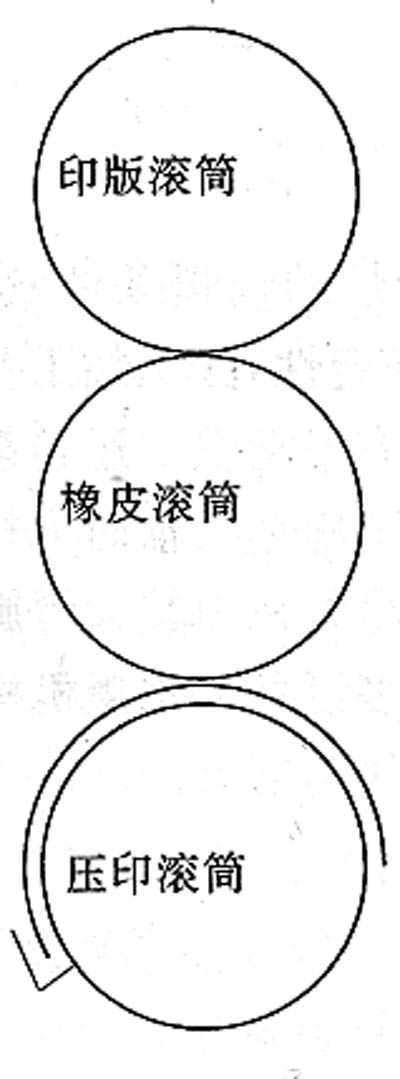
4. Commissioning of multi-unit printing unit
How to adjust the printing unit of two units or more than two units? As above, the key is the selection of the benchmark. As shown in Figure 3.23, the paper enters from the right and passes through the first unit to the second unit. From the perspective of paper transport, the first group of impression cylinders first accurately and stably conveyed the paper to ensure that the second group of impression cylinders can work normally. If the second set of transfers is not good, there is no problem with the first set of transfer, obviously can not adjust the first set of impression cylinder to meet the requirements of the second set of transfer. If the first group of impression cylinders has a problem with the transfer of paper, there is no point in shifting the second group of impression cylinders. So the second group of impression cylinders can only be adjusted relative to the first group of impression cylinders, and so on.
It can also be seen from the above figure that the first set of impression cylinders passes the paper to the transfer cylinder to reach the second group of impression cylinders. According to the transmission chain, it can be determined that the transfer cylinder is the first relative reference. The second set of impression cylinders is the second relative reference, the latter and so on. According to this relationship, during debugging, the rollers on the transfer route are first adjusted according to the reference order, and then each printing unit is adjusted. Adjustment of the printing unit is performed according to the method described above.
Geneva Watch Series Co., Ltd. , http://www.nsdigitalwatch.com