People in the CD-ROM manufacturers know that the problem of printing quality is the most, and it almost occupies the subject of the overall CD quality problem, and it is very difficult to completely solve it. The reason is that the printing production equipment has not yet been able to form an automated production line with on-line inspection like optical disc duplication. Compared with optical disc duplication, the degree of automation in printing production is not high, there is no reliable on-line inspection equipment, and the printing quality depends more on the status of the printing equipment. , the technological level of the enterprise and the technical level of the employees. Factors that affect the disc printing process include film production, stretch netting, plate making, ink distribution, printing adjustment, UV curing, and selection of screens, doctor blades, and inks. In addition, the adjustment of printing pressure and speed of the equipment, ambient temperature, and humidity are conditions that cannot be ignored.
This article analyzes some of the factors that affect the printing process, hoping to help print production of optical discs. By improving the level of printing technology, we will gradually summarize the experience of printing production, establish a standardized printing process, and improve the quality of print defects to improve the quality of the disc. CD-ROM printing is mainly screen printing and offset printing. Since there are major differences between the two methods, it will be discussed in three parts, offset printing, screen printing, and other technical common points.
1. Offset
1.1 Advantages of offset printing
The amount of network expansion is relatively small. At present, the number of outlets in the middle tone is about 7-8%. The dots of the product are full of ink and bright colors in graphic and text. The reproduction effect similar to the original film can be obtained. Therefore, it can be said that waterless offset printing has obvious advantages in controlling network expansion. Graphic and fine, colorful.
Offset printing rate is high, the printing plate can be reserved for reuse. When it is necessary to retain the printing plate, it is only necessary to clean the used printing plate with gasoline and store it in the dark. The storage time can also be greatly extended due to the convenience of retention.
Offset printing production is more automated than silk screen printing, and the process can be standardized. Therefore, the dependence on the machine is relatively large. The state of the printing equipment and the setting of parameters are the main factors affecting the printing quality. The flow properties of the inks largely affect the quality of the prints. This is because offset printing is mainly achieved by the transfer of ink.
1.2 Offset printing ink
In waterless offset printing, the quality of the ink is one of the key aspects.
Waterless offset printing equipment has high requirements on the viscosity of inks, and electrostatic phenomena are also very easy to occur. This imposes a strict requirement on the humidity in the printing peripheral environment, generally requiring humidity between 50% and 60%. The temperature control is more critical. The splitting of the ink results in heat generation, which tends to soften the ink and cause dirt on the printing plate. The temperature of the external environment during printing should generally be controlled between 18°C ​​and 22°C.
Ink has H, M, and S that are hard, medium, and soft, so that they can be used for different conditions. Alternating UV inks cannot often be used. If it is necessary to change inks, it is necessary to clean the ink fountains and ink rollers very cleanly, and remove any possible residual chemicals with a special cleaning solution.
The thickness of the ink layer has a great influence on the quality of the print. Practice has proved that the thickness of the printed ink layer is related to the viscosity and fluidity of the ink. The viscosity of the ink is too large, the ink layer is thick, and the phenomenon of pulling hair occurs during printing; the viscosity of the ink is too small, the ink layer is thin, the ink roller is easy to slip due to the rotation of the ink roller, the dots are enlarged, the image is distorted, and the surface gloss of the printed product is difference. Therefore, accurate control of ink layer thickness is an important part of quality control of printed products.
To accurately control the thickness of the ink layer, it is necessary to analyze the actual production conditions (such as the nature of the ink, the quality of the printing plate, the temperature level, the speed of the printing press, the ink absorption, and the surface smoothness, etc.). In general, under the conditions of low ambient temperature and relatively dry climatic conditions, the ink layer on the layout is thinner; on the contrary, when the temperature is high, the ink layer is thicker. When the printing surface is rough and the ink absorption is strong, the ink layer is appropriately thickened, and the layout is not easy to produce flowers. If the prints are mainly based on cable images, the ink layer should be thinner to avoid stencil printing. If printing a solid version, the ink layer should be thicker. In addition, when the printing press is fast, properly thickening the ink layer can achieve the desired ink color. In short, flexible use of the above methods in production can achieve better results.
1.3 Effect of Adjustment of Equipment Parameters
The quality of offset printing products must be reflected by ink to adjust. Therefore, in addition to the quality of the ink, the pressure between the ink supply system, particularly the ink roller, is also crucial. At the same time, the pressure between several ink rollers also has certain requirements. In addition, the pressure of the ink roller is too large. It is easy to cause dirt on the layout besides the ink bars. If the roller pressure is too small, it will cause bad ink transmission and reduce the quality of the product. The adjustment of the pressure between the uniform ink roller and the printing roller must be done strictly according to the requirements.
When the monochrome screen in the production process is large, it often encounters a situation of running color, that is, the color of different optical discs changes. The main reason is that the disc tray height deviation is too large, resulting in a change in the pressure of the printing roller, can be improved by adjusting the height of the disc tray; In addition, the cooling water temperature of the water-cooled ink is increased, the ambient temperature of the air-cooled ink changes, may make the ink The viscosity changes, causing the disc to print.
The Tennis Court Artificial Grass has soft and smooth texture and can effectively reduce skin scratches and abrasions. They are widely applies in tennis games, competitions, tennis clubs, training courts, school stadium, home use, etc.
Technical parameters of tennis court Artificial Grass
Pile height: 10mm-20mm
Gauge (inch): 3/16"
Stitch: 25-30 stitches per 10cm
Dtex: 6600
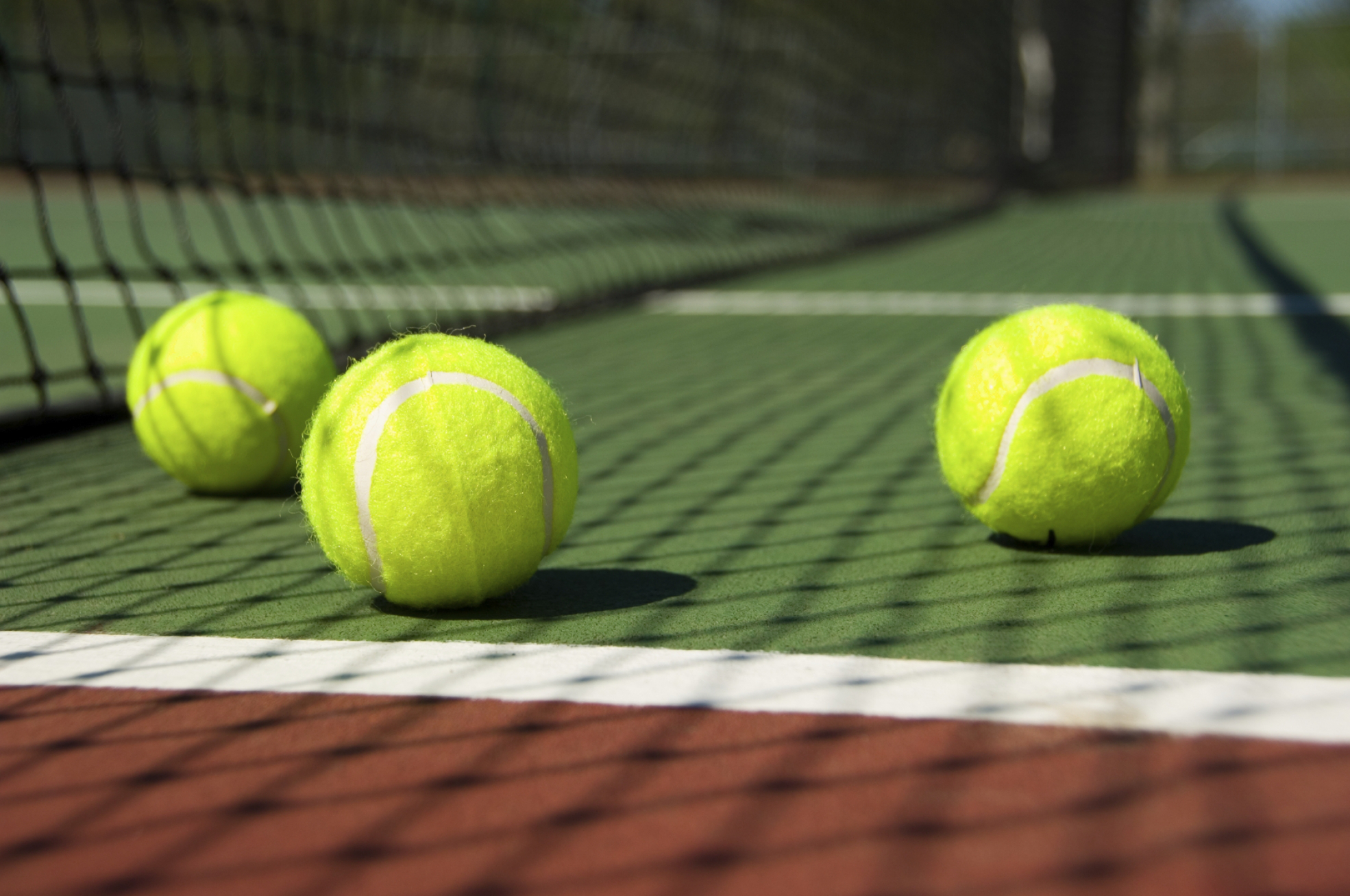
Tennis And Racetrack Grass,Tennis Court Artificial Grass,Tennis Grass,Artificial Grass For Tennis Court
Shijiazhuang Sothink Trading Co., Ltd. , http://www.chinasothink.com