The main effect of the environment is that moisture will be absorbed into components, substrates, especially solder pastes. Compared to non-clean solder pastes, water soluble wafer bumps are more sensitive to these environmental changes. If the relative humidity level exceeds 60%, moisture will enter the water-soluble solder paste; conversely, if the relative humidity is lower than 40%, it will cause the solder paste to dry prematurely. In either case, the printing performance of the solder paste will change, and the screen printing process will deviate greatly from normal and become the most affected link in the assembly process. It is recommended that the temperature be maintained between 21 °C and 25 °C, the relative humidity level be maintained between 40% and 60%; and the deviation from the set point should be minimized.
Printing press settings
Today's screen printers offer a variety of printing pressures, speeds, and separation speeds, plus the option of several different print head equipment and many modern solder paste formulations, making the selection of the right printing parameters a simple one work.
The emergence of closed printed heads brings significant benefits to the wafer bumping process. For such solder paste coating systems, the acceptable process window is wider, allowing a larger range of printing parameters to be set, thereby better controlling the overall environment of the print media to obtain high quality print results. Solder pastes with a high metal composition can be used in such systems and apply a separate coating force to inject the solder alloy material directly into the opening of the mesh plate to obtain a more perfect solder paste application shape. In general, a sufficient direct pressure should be applied to the solder paste to form a good coating point without overflowing the excess solder paste. The wiper pressure is just enough to maintain the surface of the screen clean during the entire printing process. If required, the speed of the print head can be increased beyond the limitations of the doctor blade printing method and still obtain good print definition.
Reflow oven configuration
The reflow oven of a standard surface mount assembly line is suitable for forming a solid spherical bump on the wafer surface. The industry believes that forced-convection reflow ovens with a top and bottom nitrogen ambient heating device and a low oxygen PPM level provide optimum performance. Conductive reflow ovens are also ideal for wafer processing.
Reflow oven variables may affect wafer yields and defect levels, but current experimental information is still quite limited. There is a view that the stability of the reflow process may be related to the size and orientation of the solder paste. Furthermore, the higher the percentage of wet solder paste covering the pad, the better the resistance characteristics during reflow and the more likely the solder paste will form a correct sphere on the pad.
The reflow process parameters include rapid warming up to 150°C ±10°C for the flux activation temperature stage, followed by a sharp jump to 220°C ±10°C above the liquidus temperature of the alloy, and finally to a rapid cooling phase (this is Recommendations for Sn63/Pb37 alloys). During the reflow process, the residence time of the wafer in each temperature zone is very important, and the temperature rise/fall rate should be precisely controlled according to the specifications provided by the solder paste supplier.
Remove flux residue
The longer the interval between reflow and cleaning, the more difficult it is to remove the flux.
The successful implementation of screen printing wafer bumping process requires the improvement of matching materials (such as solder paste, screens, etc.) and process design standards. In addition, important design parameters that affect the wafer bumping process include: flip chip bonding pad design, pad size/shape, pad spacing/positioning, bump lower metallization, tray design, screen design, mesh Board thickness, hole size/shape, hole orientation, and hole location. Only in-depth understanding of the numerous design strategies affecting this process can lead to excellent results.
Author: General Manager Peland Koh, DEK Asia Pacific
Kneepads Elbow Pads Palms Sports Protect
Specifications
1.New dual injection-molded flex cap design allows maximum flexibility for ease of movement and comfort
2.Minimizes gap between the bottom of the cap and plastic carrier when flexed
3.Padded side extensions for comfort and improved strap positioning
4.Contoured interior ledge secures pad positioning
5.600 Denier plastic shell
6.Closed-EPE padding provides excellent shock resistance and prevents water absorption
7.Adjustable hook and loop elastic straps
Using for knees, arms and palms protection
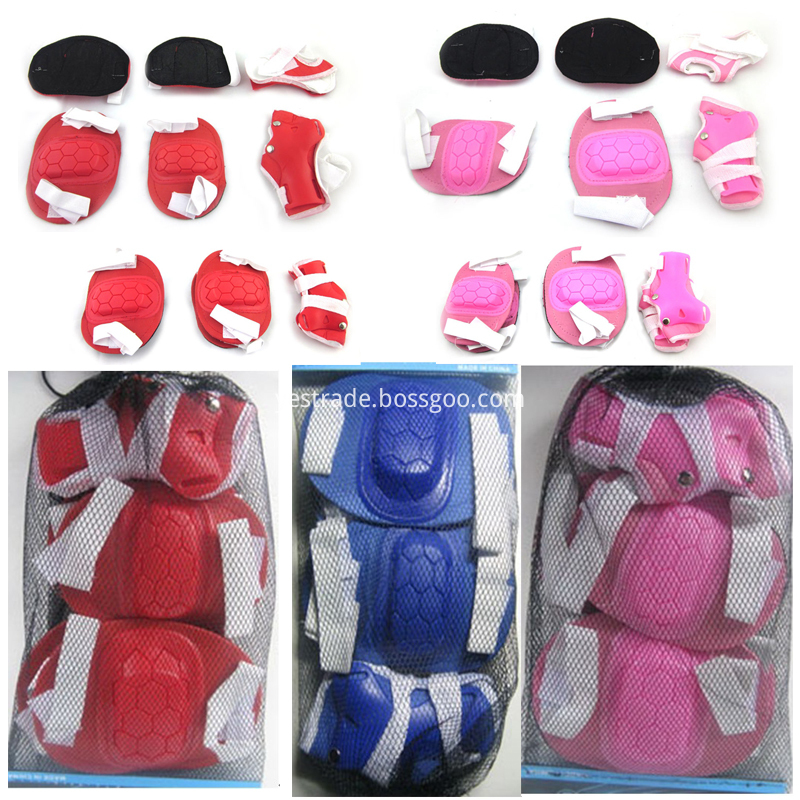
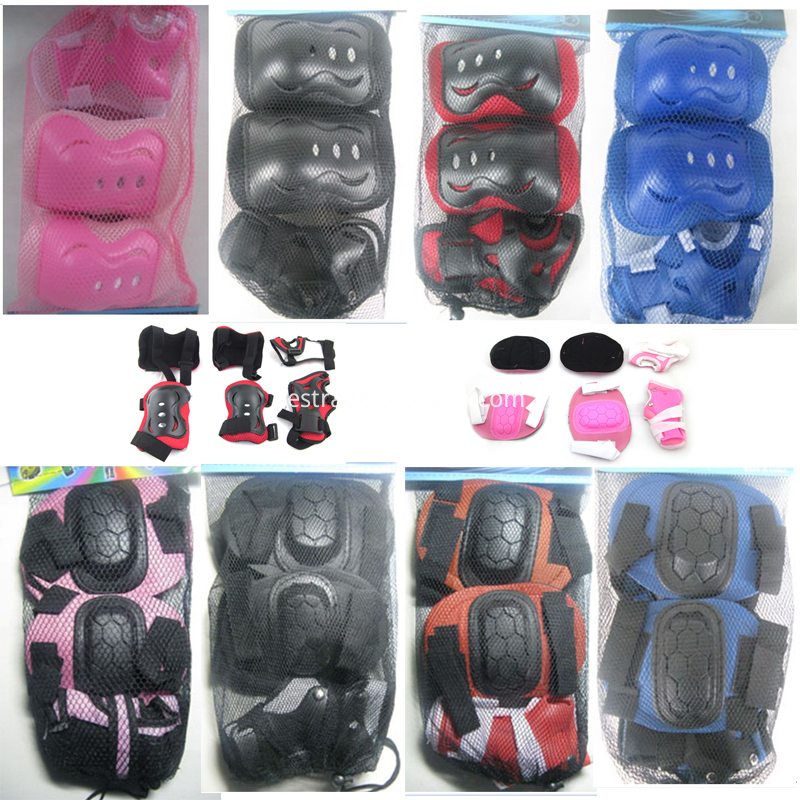
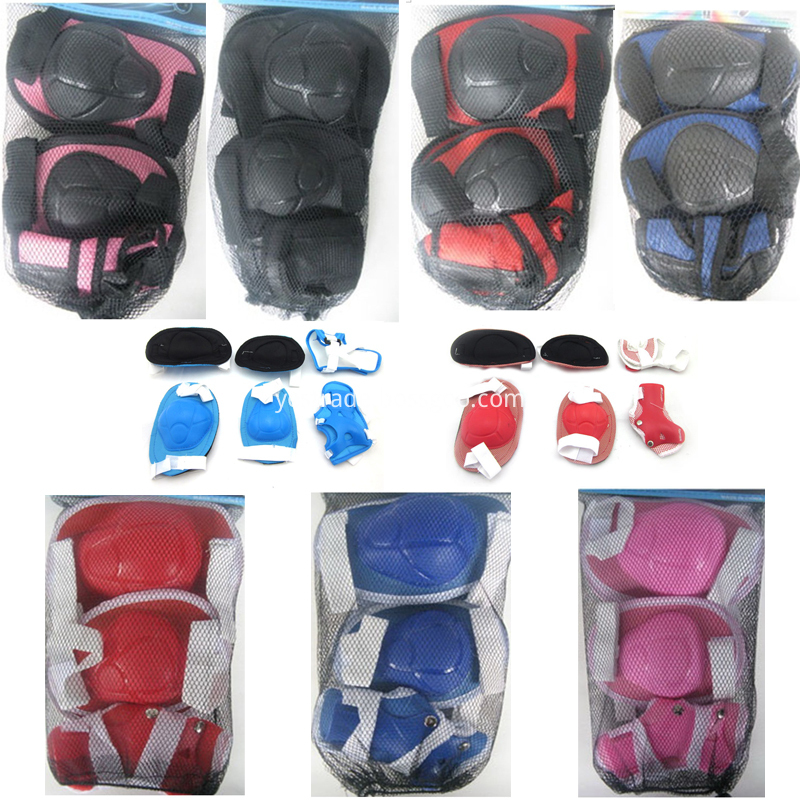
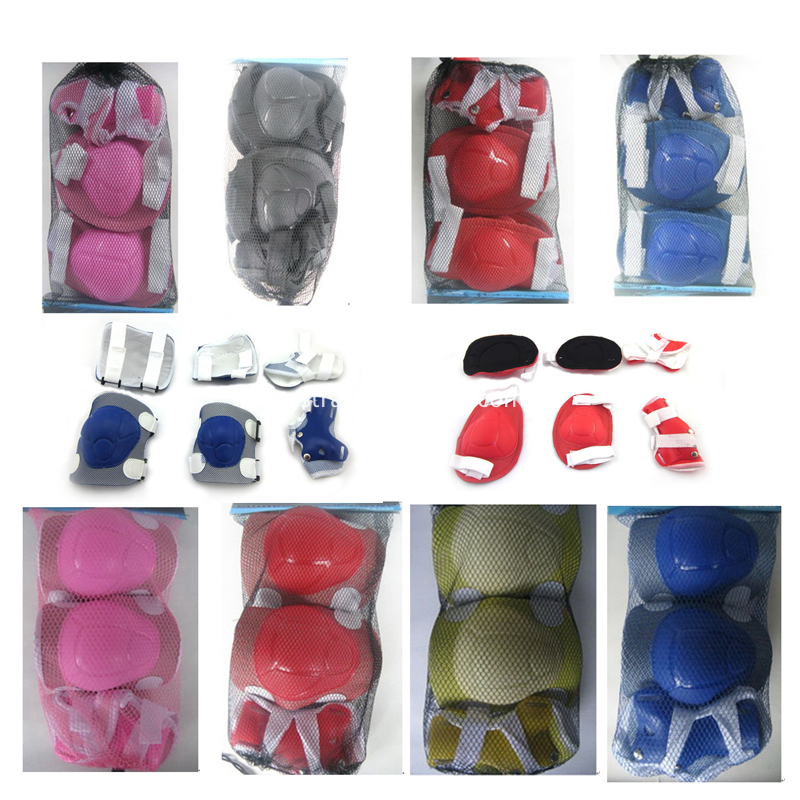
Sports Protect,Outdoor Sports Protection On Arms,Sports Protection On Knees,Kids For Outdoor Sports Protection
YONGKANG YISHANG INDUSTRY&TRADE CO.,LTD. , http://www.yes-trade.com