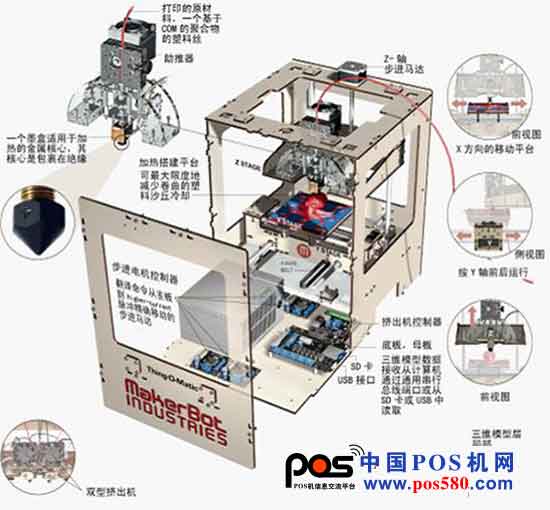
3D printer common faults:
1. The filling rate is set to 100%, and no solid objects can be printed.
The solid and hollow of the graph is irrelevant to the fill rate. The graph itself is solid and the one that is played out is solid.
2. Can't print solid objects
The model that is played out has nothing to do with the hollow and the printing software. It is based on the graphics that it draws. It is solid and it is solid. The hollowed out is hollow.
3. The nozzle is blocked, it is impossible to produce silk, how to deal with it
First check if it is the improper spacing between the print head and the bottom plate.
First clear the nozzle (Note: the new nozzle must not use the wrench to enter the nozzle inside the nozzle, just heat the nozzle to 230 ° residue will automatically flow out).
Also check if the gear and motor shaft of the extruder motor follow. If there are many motor gear powders, please clean them together.
Check if the nozzle spacing is too small, re-calibrate the platform, and also consider increasing the printing temperature by 5-10 degrees.
It is important to note that the meter must be recalibrated after the nozzle has been unblocked. Because when the nozzle is used with a wrench, the position of the nozzle may be shifted downward, resulting in a smaller and smaller platform spacing. The platform spacing is too small, when printing, it must block the wire again!
4. At the end of the print, there is sintering at the top of the model, drawing phenomenon
Set the parameters when printing, reduce the temperature of the nozzle by 5-10 degrees, the speed of the nozzle can be adjusted to 80, and the speed of the wire is changed to 100.
5. Printing can not be formed, the silk is like a ramen
This situation indicates that the distance between the print head and the bottom plate platform is too large, please recalibrate the platform.
6. During the printing process, the display of the machine is garbled, or the screen is displayed, and there is no content display?
If there is no problem with the model being printed, do not do anything and let the printer continue printing. After printing, please turn off the phone, then turn it on again, it will return to normal. This may be caused by the fact that the power connection of the printer connected to the room is not connected to the ground wire (connected to the ground wire). Consider moving the machine to a room with a normal ground connection. It is also possible that the weather is dry and the screen is caused by static electricity. This has no effect on the machine itself. If the screen is printed, the print model has gone wrong, shut down directly, and then restart the machine.
7. The nozzle does not produce silk, and the silk is pressed down by hand to output the silk.
Firstly, the nozzle is heated to 230 degrees to clean the nozzle. When the nozzle temperature reaches 230, the residue will automatically flow out. Then check whether the gear of the motor is worn due to the long-term use of the gear. For example, the gear can be worn to replace the motor gear. .
8. The sound of the nozzle is audible after entering the wire.
Because the wire is not inserted, the abnormal sound is emitted, the wire is withdrawn, and the broken wire is checked inside the motor gear, and the wire is cleaned again.
9. X-axis misalignment occurs in half of printing
First confirm whether it is printed offline or online, offline printing:
The print model is misaligned: (1) there is a problem with the motor wire or the belt, and (2) the motor wire or the switch wire signal is disturbed.
It is recommended to print a few different models to see if you can replace the new line. Generally, check if the motor cable plug and the belt are loose. Check the end and print the model. If it still doesn't work, you can consider changing the line.
Online: It may be affected by communication anomalies, such as sudden interruption of communication.
10. Operation panel keys fail
Restart the printer first (unplug the power cord, connect it, then turn it on). After a few seconds, you should be able to hear the 5-6 second startup ringtone. If you hear the ringtone, the machine can start normally, then try again. Operate the buttons. If you can't hear the ringing at boot, the machine does not start normally. At this time, you can try to press the black small round reset button on the right side of the printer, and the system will RESET.
If you still can't start the machine normally, provide a new motherboard to replace it yourself; if you can't solve it, please contact customer service to return to the factory for repair.
11. The printer does not start and the display shows two rows of barcodes.
Restart the printer first (unplug the power cord, connect it, and then turn it on) to see if it returns to normal. If it doesn't work, press the black small circle reset button on the right side of the printer and the system will RESET.
12. During the printing process, the display shows NA, then the printer stops working.
Firstly, the NA is displayed because the nozzle can't be heated. You can check whether the plug of the lower nozzle heating wire is loose. If it is checked or can't be heated, you can contact the professional document after sales to do a comprehensive inspection of the heating wire. If it is not heated after inspection. The nozzle heating line needs to be replaced.
Jiangsu Sleeptight Household Technology Co., Ltd. , https://www.sleeptightoem.com